Industria | 14.08.2024
Preventive maintenance to lower your TCO
By: Hebert Garza
14.08.2024
Share
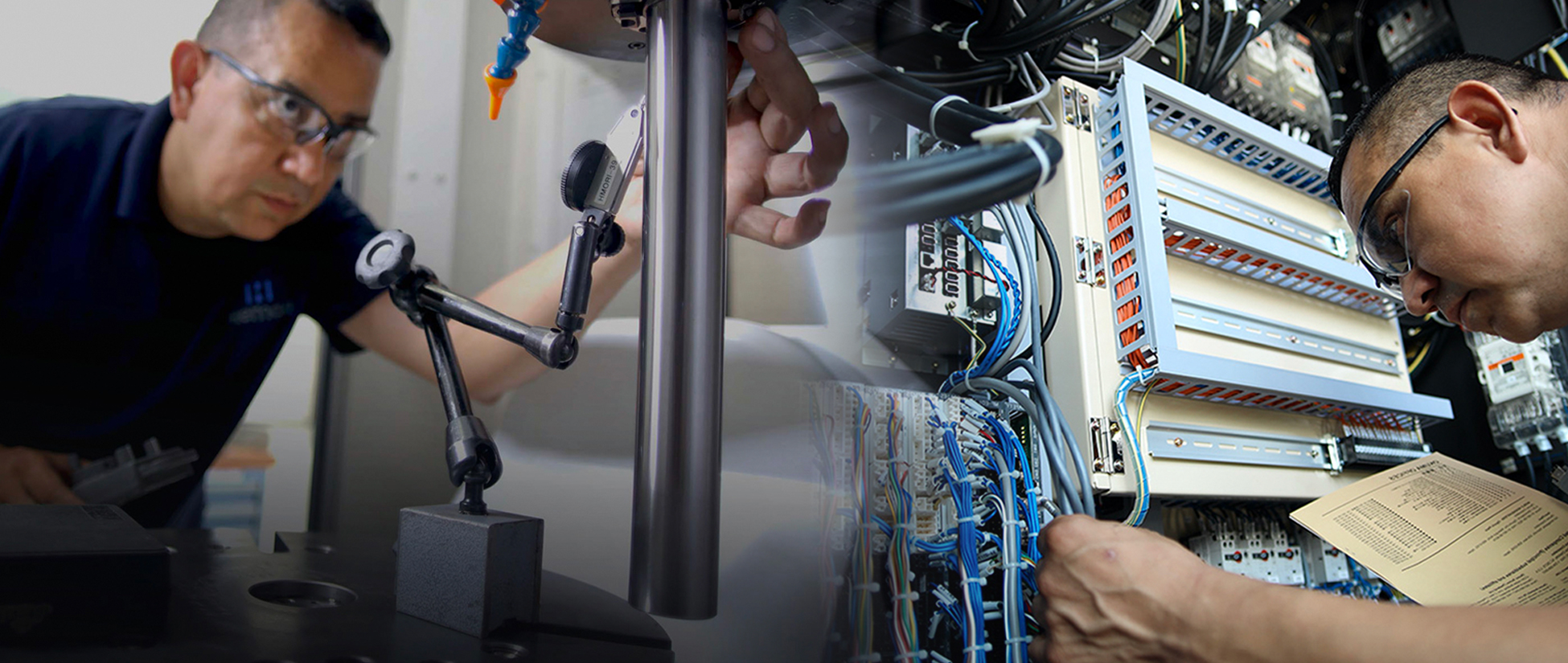
CNC Financing: One of the keys to success in the medium and long term is the protection of your investment. In the case of the manufacturing industry, the correct maintenance of equipment
—especially those that represent a considerable investment and whose repair and spare parts mean a considerable expense—, is a necessary strategy to maintain the financial health of your workshop or project.
Preventive maintenance is crucial to ensure the efficiency of your CNC equipment and that part production goals are met, and is vital to prolonging the life of your CNC lathe or machining center. Considering that everything that can fail will eventually fail, the only way to prevent costly failures and production downtime is intelligently scheduled preventive maintenance.
What are the advantages of preventive maintenance?
- Improve the efficiency of your equipment and keep its components in optimal condition.
- Increase the service life of your CNC machinery
- Prevent costly failures
- Increased safety for your operators
- Higher quality of your final product
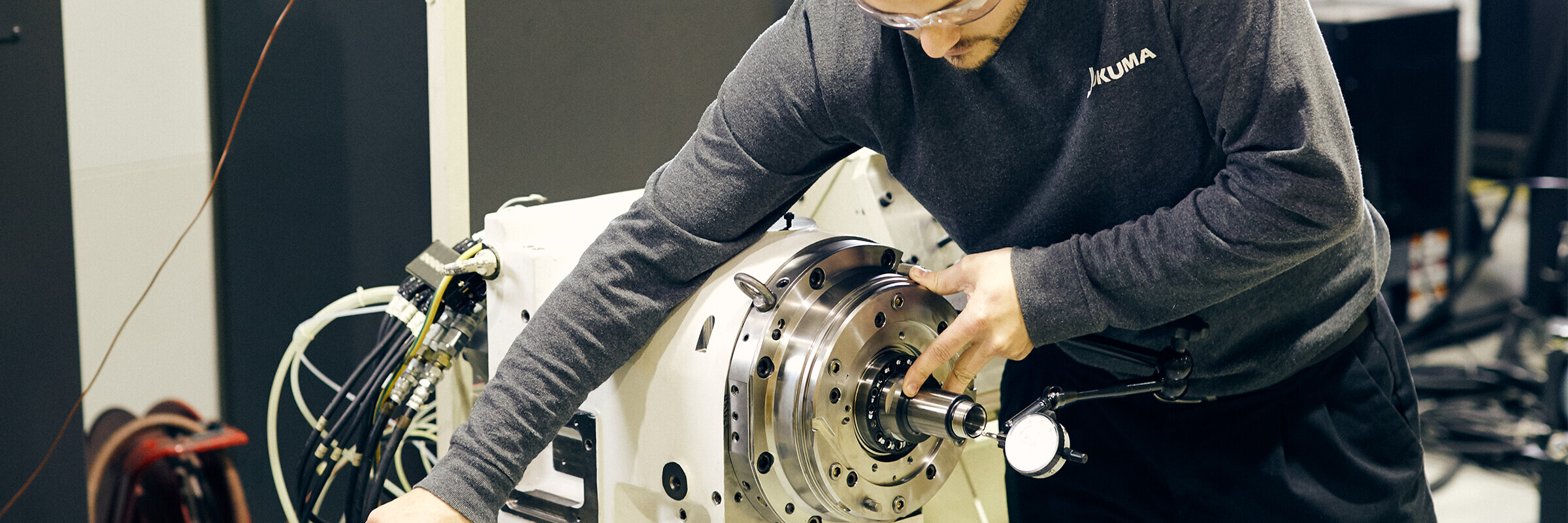
Considering all these aspects, scheduled maintenance serves as a preventive strategy to lower the total cost of ownership (TCO) of CNC equipment, because even though it adds up to short-term costs, it reduces potential expenses that could jeopardize the profitability of a piece of equipment or even a project as a whole.
TCO is defined as a tool that helps us evaluate the total costs (the sum of direct and indirect costs) associated with the purchase of CNC equipment or any other capital asset. This resource provides valuable information about the purchase cost, as well as usage and maintenance costs of the machinery.
To properly calculate the TCO of new CNC equipment, it is necessary to add “hidden” costs that are often overlooked, such as the training of your support staff and technicians. Fortunately, this “expense” can be transformed into a preventive investment by approaching experts who not only provide comprehensive solutions, but can also foresee future failures.
Other expenses to consider are operating costs and electrical and cooling consumption, adjustments to your plant infrastructure, production downtime (planned or unplanned) and possible incidents such as defective parts.
CNC Financing
In addition, let’s remember that the basic principle for the realistic calculation of the cost of ownership of a CNC equipment is based on the sum of those expenses necessary to guarantee its correct operation during the useful life of the machinery. This measure considers both one-time payment values and those expenses recurring with production, such as consumables, tooling, energy and even land use per square meter in relation to its final production.
With all these expenses in mind, having a reliable maintenance service provider with high quality standards becomes a necessity, that is, a key player to have success and profitability in your projects. Do not hesitate to contact our support team, we have at your disposal plans of service hours with no expiration date and great versatility.
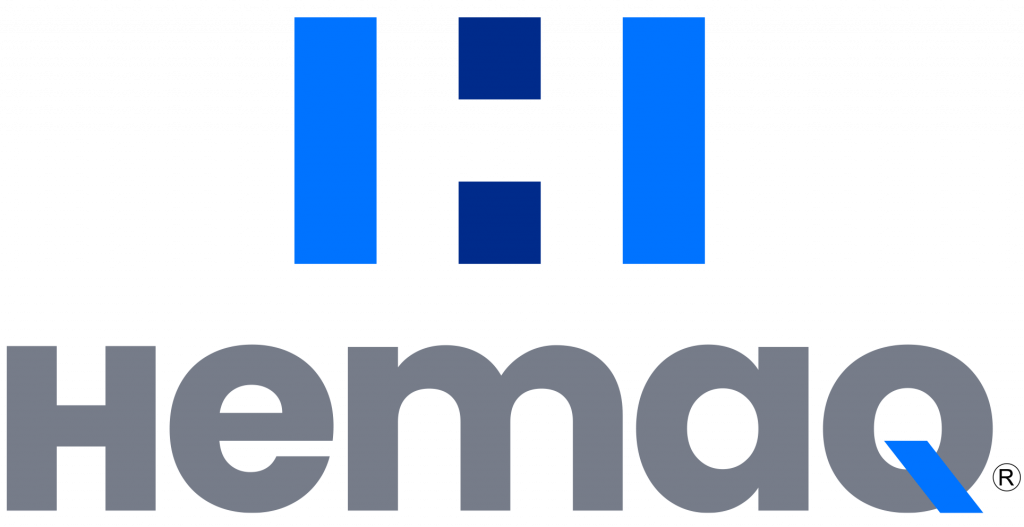