Technology | 14.10.2024
CNC Machining Centers: A Strategic Choice
By: Hebert Garza
14.10.2024
Share
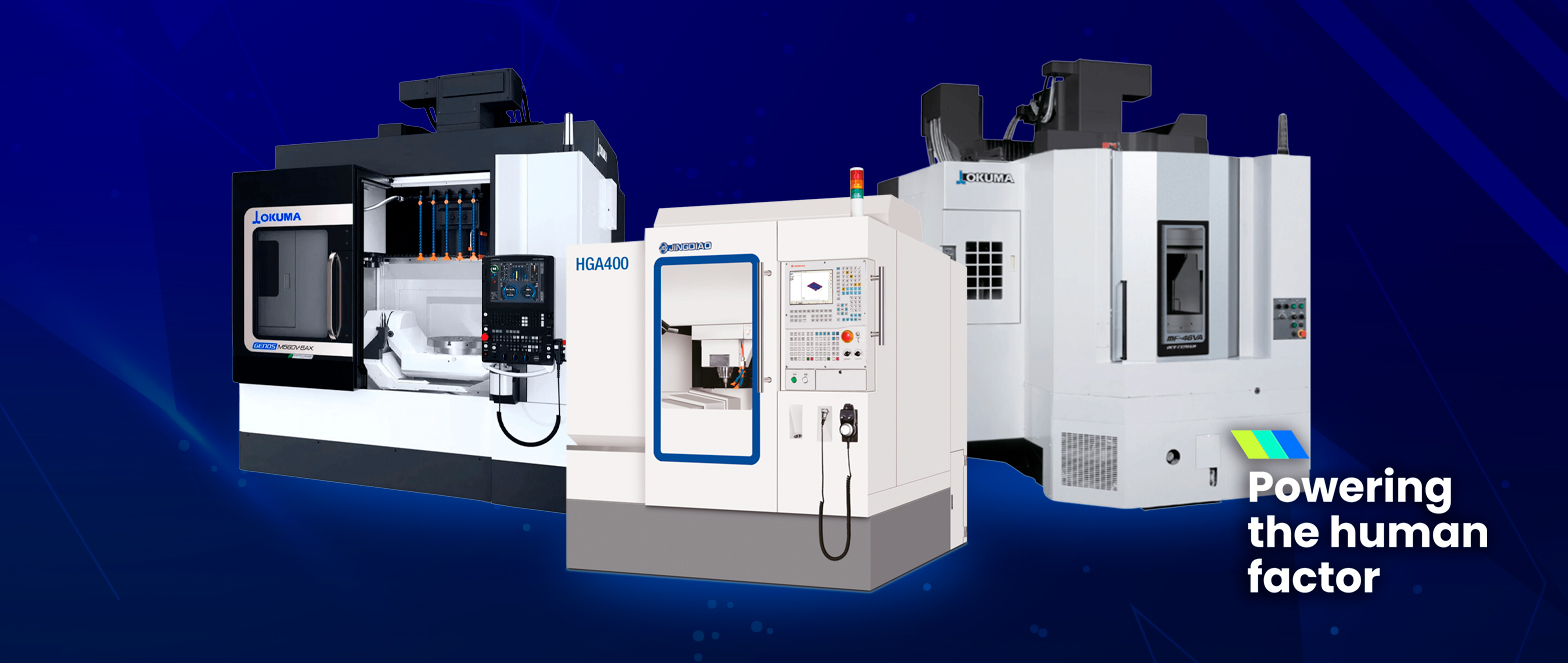
CNC Machining Centers are key equipment for modern manufacturing and industrial growth worldwide. These machines are capable of performing a wide variety of machining operations with precision and efficiency, including drilling, milling, boring, boring, routing and tapping in a variety of materials. In this article, we will examine the different types of CNC Machining Centers available on the market and their specific applications within the manufacturing industry. In addition, we will explore their importance in today’s production context and how they can improve the competitiveness of companies.
Vertical Machining Centers
The Importance of CNC Machining Centers in Modern Industry
In addition, CNC Machining Centers are highly automated, which means they can operate continuously and reduce the need for manual intervention. This not only minimizes the risk of errors, but also optimizes the use of resources, allowing operators to concentrate on more strategic tasks within the production process.
Successful examples in the use of CNC Machining Centers
Numerous companies have adopted CNC Machining Centers to improve their competitiveness. For example, in the automotive industry, renowned manufacturers have implemented these machines to produce critical components such as engine blocks and cylinder heads with unprecedented precision. This adoption of technology has led to shorter lead times and improved product quality.
CNC Machining Centers have revolutionized the way products are manufactured in a variety of industries. Thanks to their ability to perform complex operations and their high precision, these machines enable manufacturers to reduce production time and improve the quality of the final product. This translates into increased customer satisfaction and improved profitability for companies.
Benefits of Automation in CNC Machining Centers
These are the most common equipment due to their versatility and ease of operation. Their vertically oriented spindle allows machining flat surfaces and cavities in fixed parts on the worktable, so they are widely used in the manufacture of molds, dies and medium-sized components.
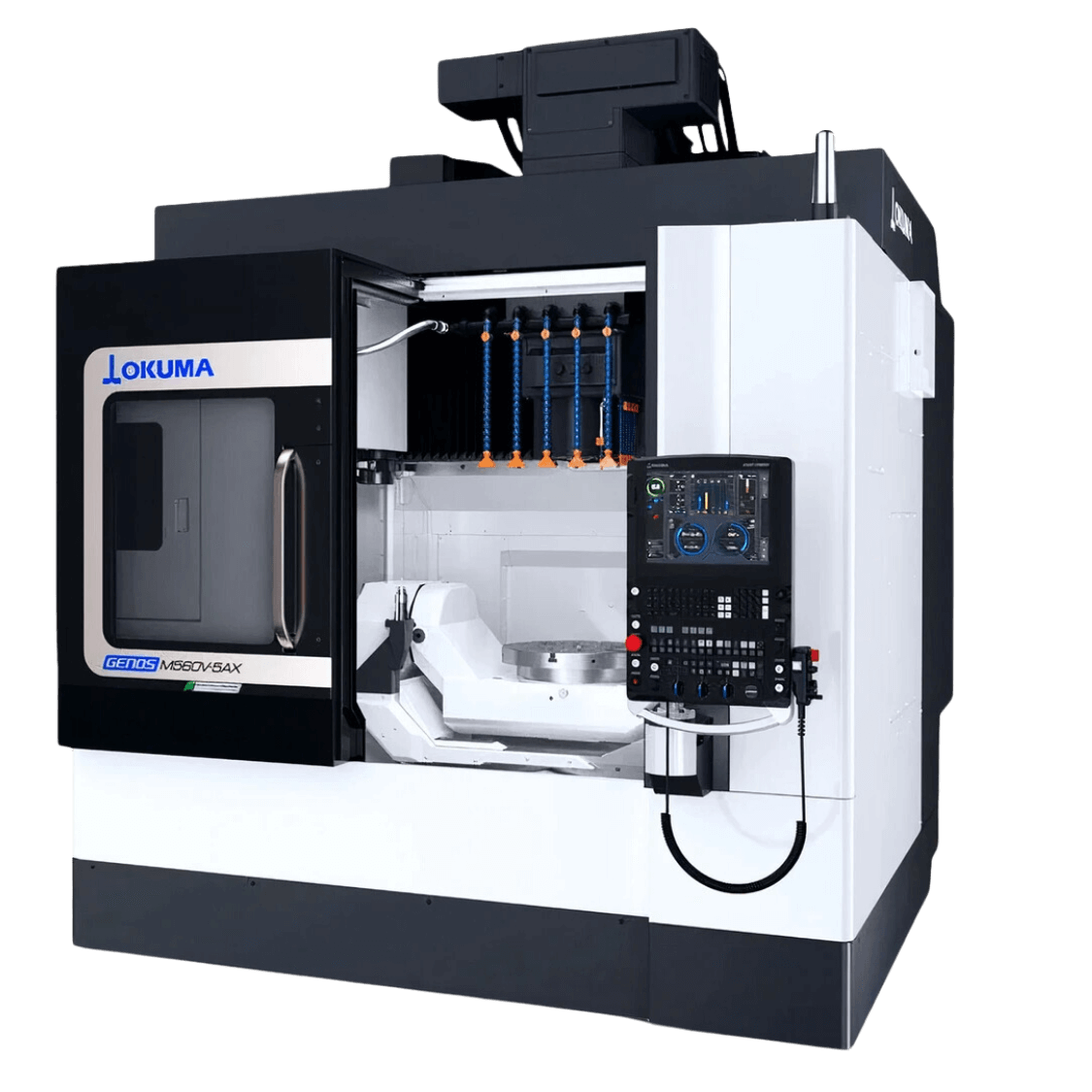
Applications
- Automotive industry: manufacturing engine blocks, cylinder heads and chassis parts.
- Aerospace industry: machining of structural components and airframe parts.
- Mold and die manufacturing: production of plastic injection molds and metal stamping dies.
The future of CNC Machining Centers
As technology advances, CNC Machining Centers continue to evolve. The integration of artificial intelligence and machine learning promises to take automation to a new level. This will allow for greater customization in production and continuous improvement in operational efficiency.
Advantages
- Lower cost compared to horizontal machining centers.
- Easy setup and operation.
- Suitable for machining small and medium size parts.
Horizontal Machining Centers
The arrangement of the spindle in this equipment facilitates access to the parts from different angles, making it more comfortable for operators, and the chip or burr is more easily removed during machining, which improves the efficiency and quality of the work. Also, these offer the possibility of machining several sides of a part with a single clamping and the use of different pallets, which increases the productivity of the project.
Applications
- Gas and Oil industry: machining valves, pumps and other large components.
- Heavy machinery manufacturing: machining of gearboxes, frames and other excavator components.
- Mass production: machining of high-volume parts with high precision, such as transmissions and gearboxes.
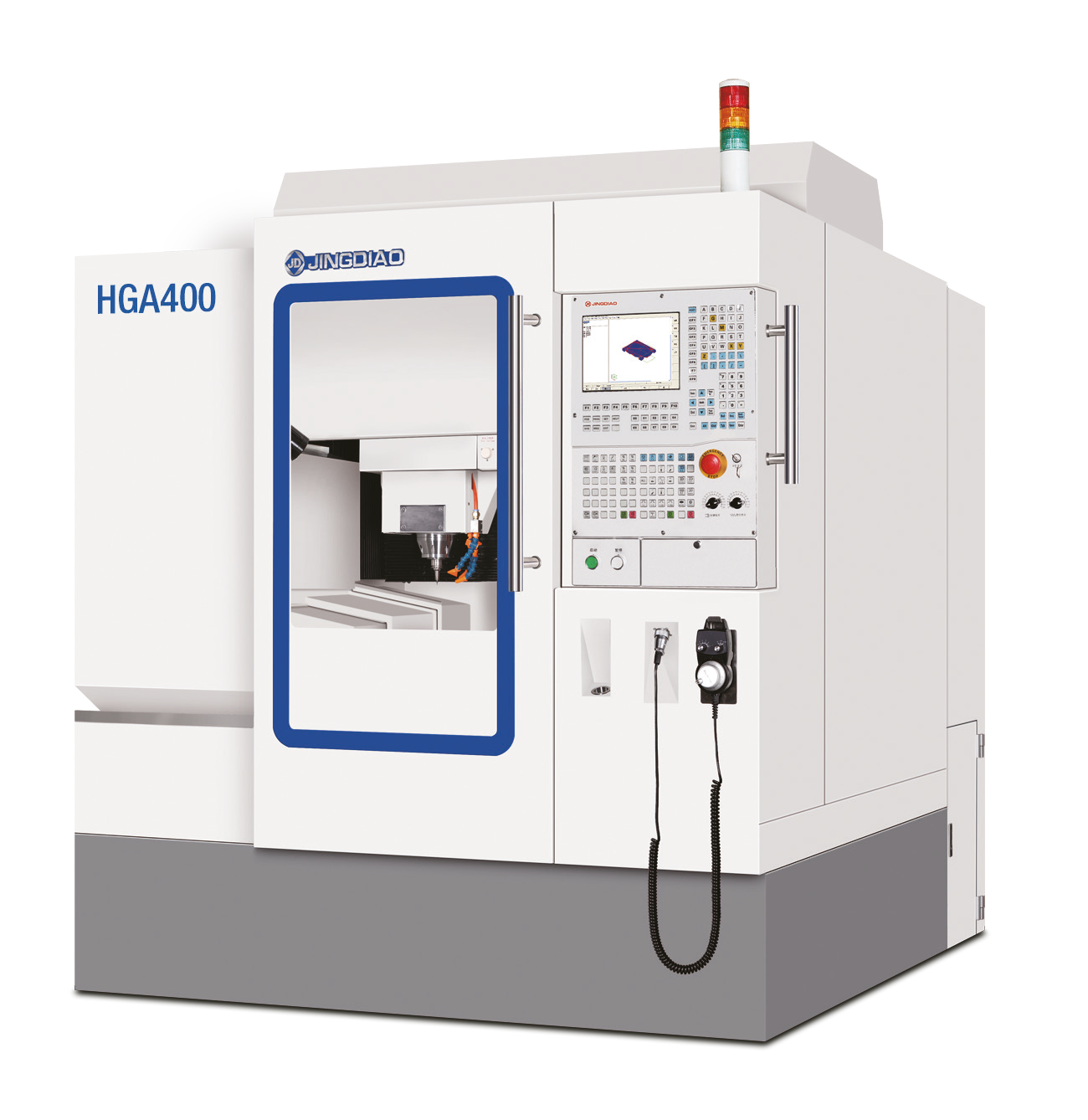
5-Axis Machining Centers
This equipment allows rotation and movement of the tool in the three traditional axes (X, Y, Z) and two additional axes, making it possible to machine parts with complex geometries in a single setup, reducing production costs and improving machining accuracy.
Applications:
- Aerospace industry: manufacturing engine parts and aerodynamic components.
- Medical industry: production of orthopedic implants, prostheses and surgical tools.
- Complex mold industry: creation of molds with complex geometries in a single operation.
Multi-Tasking Machining Centers
Multi-Tasking Machining Centers combine turning, milling and drilling operations, among other techniques. They are ideal for machining complex parts that require different operations without the need of other machine tools, thus reducing production time and costs.
Applications:
- Medical industry: production of components for medical equipment and surgical devices.
- Aerospace industry: machining complex and tight tolerance parts.
- Machine manufacturing: machining of parts that require multiple operations.
Advantages:
- High flexibility for a variety of parts and operations.
- Reduced set-up times between different types of jobs.
- Ideal for mixed production shops.
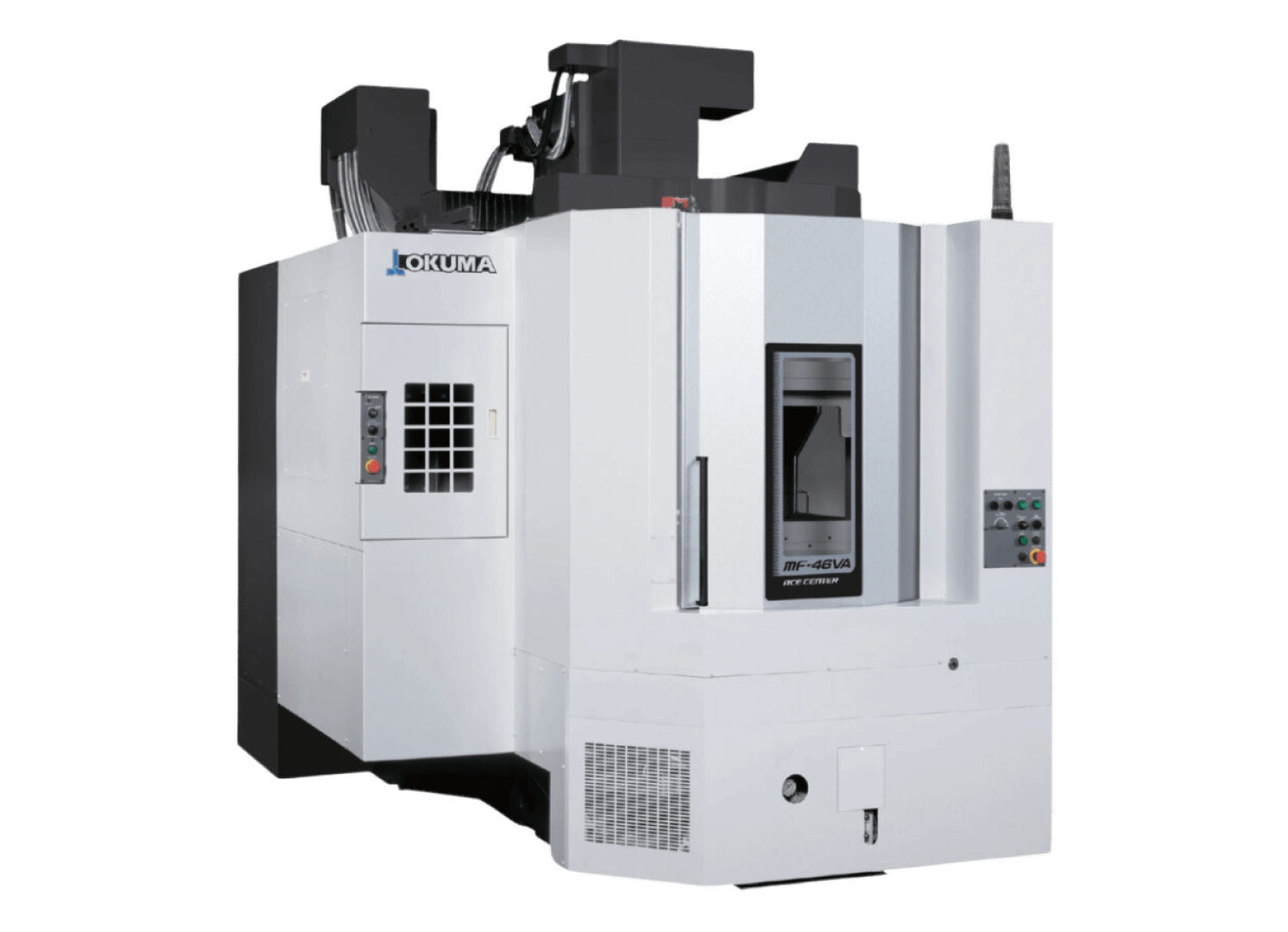
In addition to helping you choose the ideal equipment for your project, our commitment is to find the best configurations of tools, accessories and peripherals for your project; as well as to guide you during project implementation and provide you with qualified technical support 24 hours a day, 365 days a year.
Our goal is to deliver quality, excellence, robustness and precision in each CNC Equipment in our catalog, in this way we seek to ensure you improve your manufacturing processes through Machine Tools and technical support services with the highest technology.
In addition, industrial connectivity, known as Industry 4.0, is enabling this equipment to communicate with each other and with other production systems, further optimizing workflow and real-time decision making. This is essential for companies seeking to remain competitive in an increasingly complex and demanding production environment.
Conclusions
CNC Machining Centers represent a crucial investment for any company looking to improve its production capacity. Not only do they offer versatility and precision, but they are also fundamental to the automation and modernization of manufacturing processes. With their continued development, these machines are likely to become the industry standard, helping companies meet current and future market challenges.
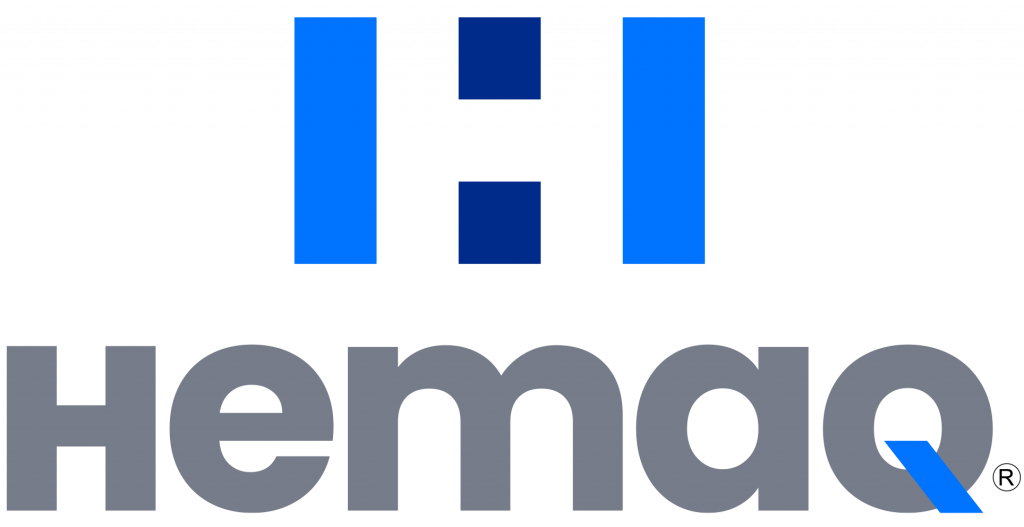