Technology | 21.10.2024
Key considerations when choosing your CNC Lathe
By: Hebert Garza
21.10.2024
Share
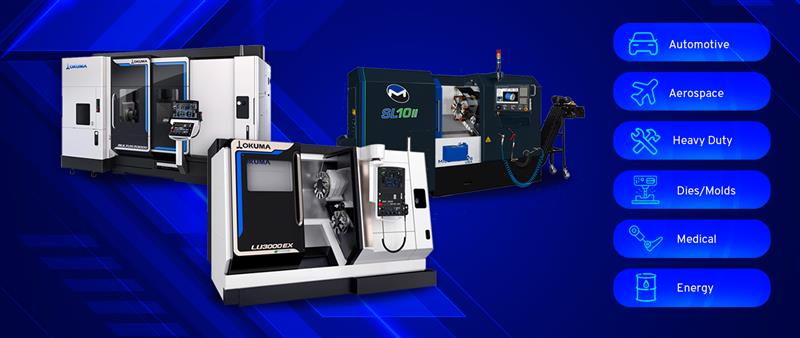
The CNC lathes are an essential pieces of equipment for any modern manufacturing plant or shop, as it allows precise and automatic machining, as it is an easy to program and operate machine tool. When choosing the right CNC lathe for your project, it is important to consider several aspects to ensure that it fits your production needs and helps you maximize your shop’s operational efficiency.
Lathe size and capacity
It is critical to evaluate the size of the parts to be machined. CNC lathes vary in terms of machining capacity, so it is crucial to select one that can handle the maximum diameter and length of the project parts. In addition, the space available in the shop to accommodate the machine and its layout relative to other equipment must be considered.
Control type and software
CNC lathes operate under different control systems, for example, Okuma CNC lathes work with different variants of the OSP control, with the OSP-P500 being the latest version available. While other brands might use Fanuc or Siemens numerical controls. The choice of system will depend on both the operator’s preference and compatibility with the CAD/CAM software used. A system that is intuitive and easy to program will reduce learning time and improve productivity; for example, a shop with several Okuma machine tools will have the advantage of reduced lead times and greater efficiency.
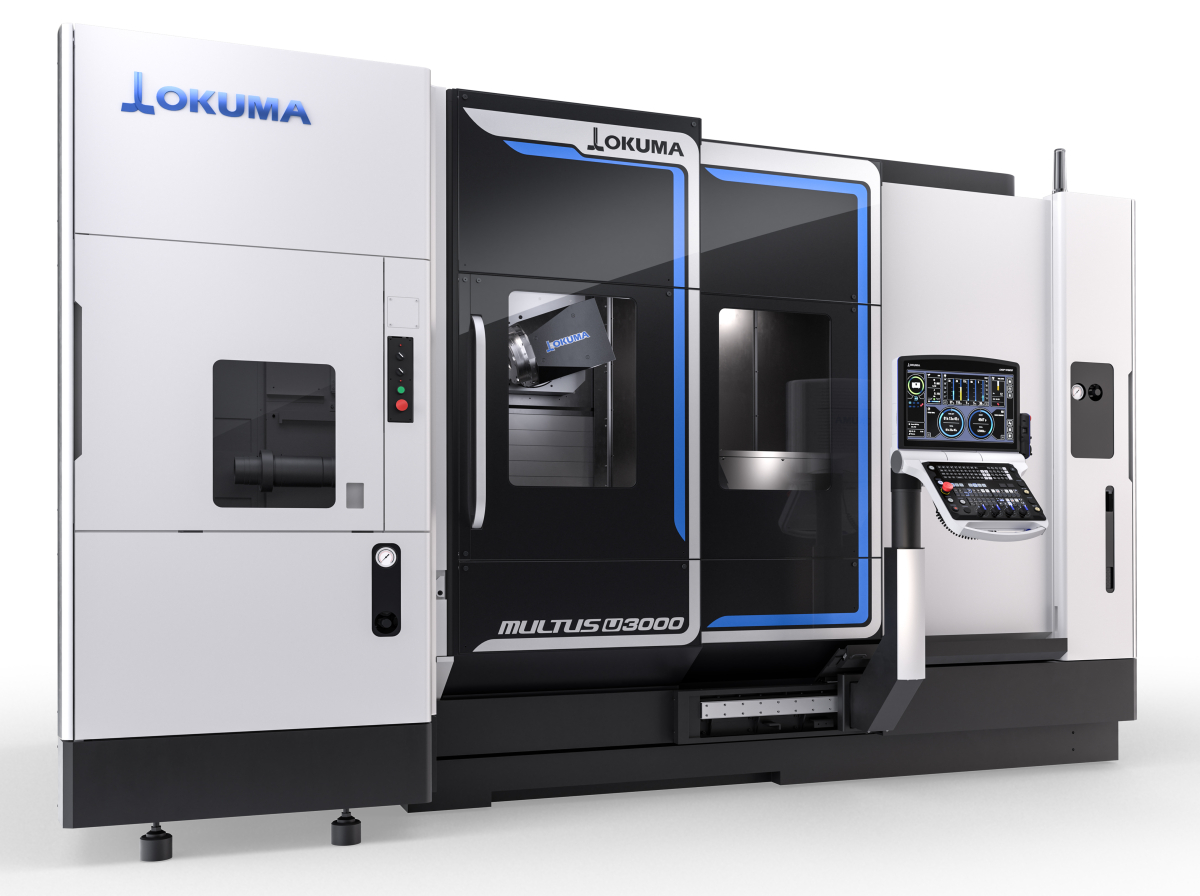
Number of axis
Traditional CNC lathes typically have two axis (X and Z), but if the job requires more complex geometries, lathes with additional axis (such as Y and C) are an option. These allow milling and other advanced operations to be performed in a single setup, improving efficiency and accuracy. Also, opting for CNC lathes with extra axis and higher precision capabilities can mean greater profitability, as they are flexible for other machining projects.
Spindle speed and power
Spindle speed and spindle power are decisive for the type of material to be machined. Harder materials require more power and a robust spindle, while for small, precise parts, speed is a key factor. A safe approach to determining these variables for your project is to consult with a team of experienced engineers. In our case, our partners and customers are assured of the best advice available in the market, and our engineering team provides advice on equipment, tooling, accessories, peripherals and even automation systems, ensuring an efficient and cost-effective project.
Automation and additional accessories
Modern CNC lathes can include automatic functions such as bar loaders, automatic turrets or in-process gauging systems (in-process gauging) systems. These accessories increase productivity by reducing manual intervention and ensuring greater accuracy in continuous operations. These options can be loading and unloading, but systems can also be added with other CNC machine tools to reduce production times. For more information on our Automation systems available, please visit www.otomatiqa.com/en.
Technical service and after-sales support
Good technical support is crucial. The complexity of CNC lathes means that any unexpected downtime can lead to financial losses. The solution to this is to have 24/7 support from a team of experienced engineers and technicians, as well as after-sales support that includes quick technical assistance and spare parts with a sense of urgency and easy access.
Conclusion
Investing time in evaluating all these aspects will ensure a choice that maximizes the productivity of your project and minimizes long-term costs. At HEMAQ we believe in our customers and their projects, because our philosophy is focused on creating productive relationships of trust. With us, you will be able to find Integral Solutions for all your machining needs, because we have the best brands worldwide chosen based on a thorough evaluation; in addition to 24/7 Support and more than 36 years of experience.
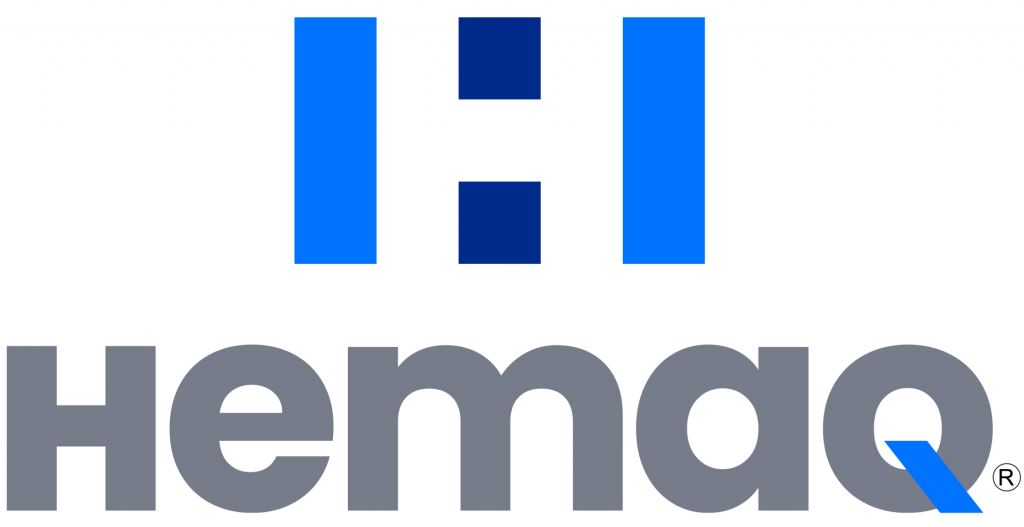