Technology | 16.01.2025
The Importance of Preventive Maintenance on Lathes and CNC Machining Centers: Common Problems and Solutions
By: Gilberto Acosta, Gerente de Servicio México Sur y Centroamérica
16.01.2025
Share
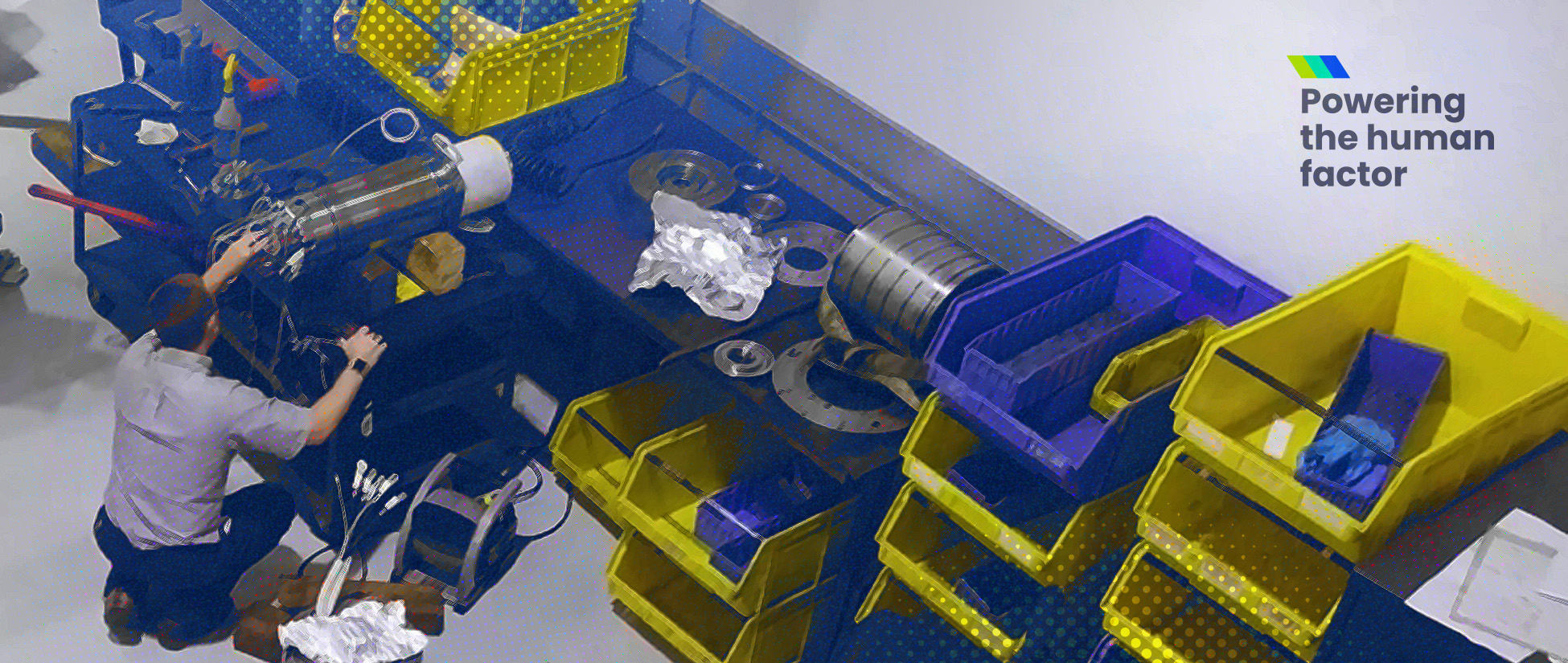
Although CNC Lathes and CNC Machining Centers are essential for the production of high precision machining in the industrial sector, the lack of preventive maintenance can cause serious problems that can affect and even stop productivity, degrade product quality and increase operating costs. Below, we explore the main problems resulting from the lack of maintenance on lathes and CNC machining centers and the solutions to prevent them.
Main issues caused by lack of maintenance
1. Premature component wear
The accumulation of dirt, chips and degraded lubricants can accelerate the wear of key CNC equipment parts such as spindles, linear guides and ballscrews. This reduces equipment life and increases repair costs.
2. Failure of electrical and electronic systems
The control systems, electronic boards, speed controllers and sensors of CNC equipment are highly sensitive. Dust and moisture buildup can cause short circuits, system errors and intermittent failures that stop production.
3. Loss of accuracy
Lack of regular adjustments, calibrations and geometry verification causes deviations in the accuracy of your CNC equipment including lathes, which can result in defective, out-of-specification parts and material waste.
4. Increased downtime
Unexpected breakdowns cause production stoppages that affect delivery times and increase operating costs due to the need for emergency repairs, in addition to other expenses generated by the purchase of damaged components.
5. High energy consumption
CNC equipment like lathes, lacks the necessary preventive maintenance activities operates inefficiently, consuming more energy and generating additional costs for the company, as well as deficiencies in the machining process.
Effective solutions to prevent these problems
1. Implement a preventive maintenance plan.
A well-structured plan includes periodic inspections, thorough cleaning, lubrication of components and regular calibrations. This helps identify potential problems before they become serious failures.
2. Train personnel
Extensive and adequate training for your operators and maintenance personnel by a team of experts is vital to improve the performance of your machine tools.
3. Use quality spare parts and consumables
The use of original parts and consumables recommended by the manufacturer ensures optimum performance and reduces the risk of failure. A supplier that guarantees the authenticity of the parts is a key ally to keep your equipment in optimal conditions.
4. Continuous monitoring
Incorporating monitoring systems to supervise equipment status in real time allows detecting abnormalities such as excessive vibrations, overheating or component wear, such failures can be redirected to a 24/7 support service to avoid unnecessary shutdowns.
5. Collaborate with maintenance experts
Hiring specialized CNC maintenance services ensures that your equipment receives the attention it needs. Our experts have advanced tools and the experience necessary to perform accurate diagnostics.
Benefits of keeping your CNC equipment in top condition
Proper preventive maintenance not only avoids technical problems, but also:
- Prolongs the useful life of the equipment
- Improves the quality of manufactured products
- Reduces operating costs
- Increases productivity and energy efficiency
- Helps meet delivery schedules and customer expectations
For lathes and other equipment:
Contact our experts to ensure the maintenance of your CNC lathes and CNC machining centers as a strategic investment. Implementing a preventive maintenance plan and having trained personnel are essential steps to avoid problems and maximize the performance of your equipment. Do not underestimate the importance of maintenance: a well-maintained equipment is synonymous of success in your operation.
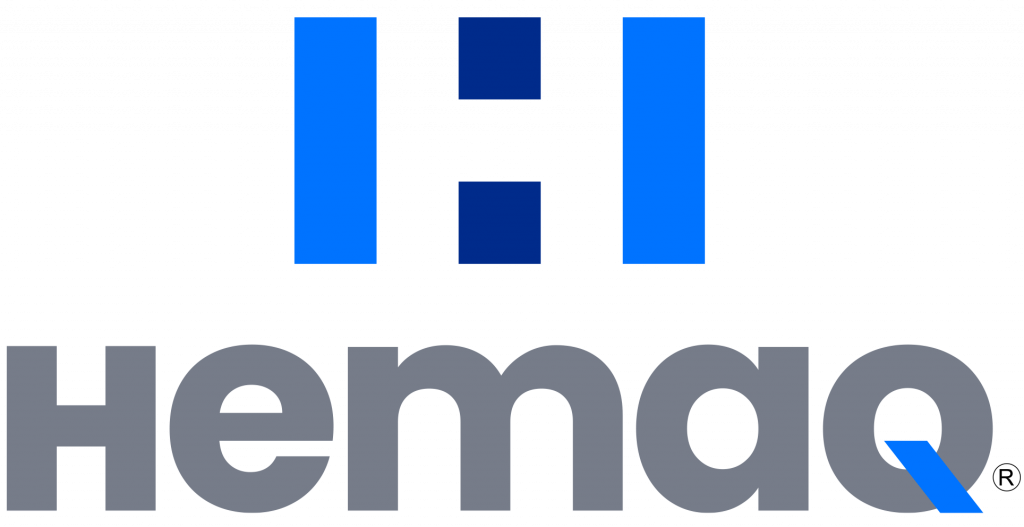